
Membrane Technology for
Post-Combustion Carbon Capture from Coal-Fired Power Plants
Group 2: Tim Becker, Hye-In Son, Angel Asante, Nadeeka Karunaratne
TECHNICAL FEASIBILITY
In order to make this process not only economically feasible, but also technologically feasible, we must investigate factors that will influence the CO2 separation with membranes:
All of these factors are important and must be considered to gauge how feasible this
technology is for carbon-capture applications.
Two-Step Counter-Flow/Sweep System
Assessing the technical feasibility of using CO2 capture membranes in a specific process genereates more information that cannot be obtained when looking at membranes in general.
The following takes gives an overview of the cost of capture and energy requirements for the use of membranes in the Two-Step Counter-Flow/Sweep System.
The recent work of Richard Baker in conjunction with the U.S. Department Energy has allowd for the creation of membranes with CO2 permeances >1000 gpu and CO2/N2 selectivities of 50 at 30◦ C. This permeance is ten times higher than commercial CO2 membranes and the selectivity is among the highest reported for non-facilitated transport materials. These membranes, in combination with a novel “Two-Step Counter-Flow/Sweep System“ (shown in Figure 1 below) process design that uses incoming combustion air as a sweep gas to generate driving force, could help meet DOE CO2 capture cost targets of 90% separation, 95% CO2 purity. This procusses has low energy requirements because it uses incoming combustion air as a sweep to generate driving force for CO2 separation. In this way, the sweep module avoids the energy penalty of compression or vacuum treatment and provides an essentially “free” separation. (Baker et al 2010)
A number of sensitivity studies were done to optimize the process in Figure 1 for a 600 MWe coal-fired power plant. The optimum balance of low-energy use and low capture cost occurs at pressure ratios of 5–10 for this process. For a feed pressure = 2.0 bar, and permeate pressure = 0.2 bar the following information on energy and power consumption were found:
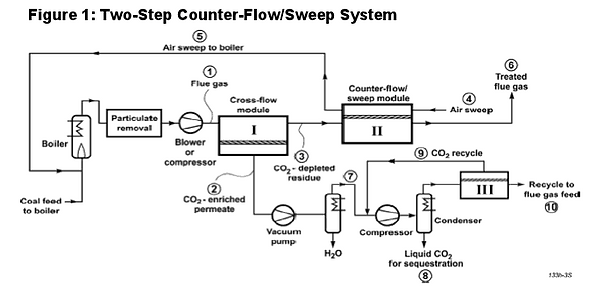
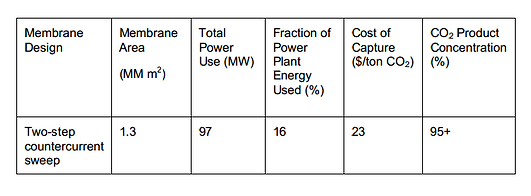
Factors which limit CO2 separation technology include:
-
Flue gas contaminants- the effects of flue gas contaminants (such as fly ash,
SO2, NOx, trace metals) on membrane separation have not been considered or
researched extensively in this context -
Impact of higher CO2 content in the boiler- Because low-energy processes
such as the Two-Step Counter-Flow/Sweep System burnig coal with sweep air
containing CO2, the impacts of high CO2 contents on separation efficiency must
be looked at. -
Reliability Issues - How likely is it for holes to form in the membrane itself? Can
contaminants easily clog the membrane after continuous use? What about the
interaction of the contaminants with the membrane material? -
Uncertain Lifetime - it’s uncertain how reliable membranes are for post-
combustion CC over long periods of time